As part of our tour of Huawei’s China facilities, we were given an exclusive look at the company’s Research & Development labs. In the second of a two part-series, we look at the ways that Huawei tests the ability of its handsets to survive environment and climate changes as well as the key part; the reliability of its smartphones and their various ports and buttons.
In the first part of this series, we covered how Huawei tests its handsets for network performance and compliance with radiation emissions regulations and in this second part, we’re going to look at the tests that really affect mobile handsets – the reliability of the handset and its ports and the ability of the handset to handle different environments and climate changing.
Climate and Environment Testing
As a global business, Huawei’s handsets are approved for use in many different markets around the world making the environment testing crucial to the success of its devices business. From the tropical heat of the Middle East and Asia to the freezing weather in Russia and the ever-changing climate in the West, a smartphone needs to be able to handle different heats.
Huawei conducts its climate testing in a room that can be best described as a large warehouse containing several cubes, each of which is designed to simulate a different environment. The cubes are seal-proof to ensure that the climate testing cannot be influenced by external forces.
The largest cube is 17 cubic metres and is large enough to fit an elephant and the room contains cubes of different sizes from small to large. The highest temperature of the rooms is 61°C whilst the lowest temperature is -40°C and these allow the company to test Huawei smartphones to ensure they can operate between -20°C (somewhere like Russia or the Nordics in the winter) to 55°C (the Middle East at the height of the summer). Each handset tested has to survive between these temperatures in order for the test to be considered a pass.
Testing the environment and ability of smartphone to acclimatise is crucial as it helps ensure that when you take your phone to a foreign country where the weather may be one of the two extremes, you’re able to use and carry it safely. However, the handset also has to be satisfactory for use and now we’ll take a look at how Huawei tests the reliability of its smartphones including their ports and connectors.
Device Reliability Testing
Now we come to arguably my favourite part of the tour of China – seeing how Huawei handsets are tested. Each handset undergoes a series of tests with some tests taking up to five days to complete. We were given a special demonstration on eight tests which vary from testing the ability of the phone to handle a drop to the reliability of the USB connector, headphone jack and power button.
Mechanical Stress Test is used to test the structural reliability of a handset and is performed on every smartphone (in the test batch). In layman’s terms, this test checks whether a handset is capable of structurally surviving a drop and each handset is dropped 100 times at heights of both 0.5 metres and 1 metre to test whether it is structurally sound.
The test contains five rounds of iteration; the first round features the freshly designed handset with no prior testing and as each round reveals a defect, improvements are made before the next iteration is tested. From each batch of handsets, there are ten units selected and each is dropped from the two heights which simulating dropping your phone from your pocket (0.5 metres) and dropping your phone from your hand (1 metre). For the batch to pass, all of handsets tested need to pass.
As long as there are no defects found, the handset is considered to have passed the test at the end of the first iteration of testing. The machine used in the test was sizeable and the sound emitted by the handset as it spun around the insides suggested it was hitting the panels with considerable force.
Button Test measures the performance of the power and volume keys. The process is largely automated with mechanical shutter pressing the power button 200,000 times and another machine testing each of the volume keys 50,000 times.
In the button testing, there are five rounds of iteration with the first three somewhat lenient and the last two requiring complete passes. During the first three tests, handsets with small faults may still be considered a pass as long as they are fixed before the next round of iteration but in the final two tests, all handsets need to pass each test with no faults.
Connector Test checks the reliability of the USB connector and headphone jacks to fix a common problem. The vast majority of smartphones and tablets use a microUSB port and the unreliability of USB ports and the headphone jack is a well documented issue. Often on most devices – although some brands are at fault more than others – it can be difficult to easily insert the microUSB cable into the USB port and the headphones into their jack or the ports would cease to work.
The test aims to prevent this and takes place over two machines – one inserts and removes the USB 10,000 times and the other inserts and removes the headphone jack 5,000 times. On average, a person will insert their charger into their handset once a day and the test is simulating the USB cable being inserted every day for 27 years.
The test also stretches and twists the USB cable (when connected to the handset) in different directions to ensure the USB port continues to work. The USB connector test is an in-house Huawei patented test which, combined with the extensive testing, is why Huawei guarantee the USB connector will work for three years.
Soft Pressure Test is one of the strictest tests in the room with zero malfunction allowed. It tests the ability of the handset to continue working after being bent. Each handset is tested 100 times with a force of 25kg and during the testing, you can physically see a handset being bent and continue to work afterwards (we wouldn’t recommend you trying this at home!)
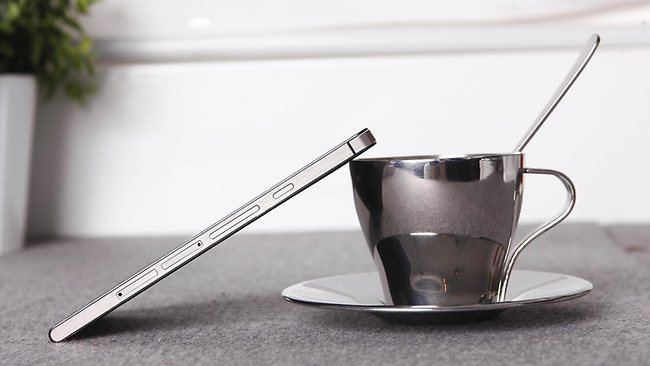
Soft Press Tiredness Test looks after the scenario where you drop your phone and accidentally step on it. The handset sits on a plate which rests between two clamps and a force of 70kg pressure is applied to each handset once. If the handset survives the force, it’s considered a pass.
Twist tester is enjoyable to watch as the machine twists the handset in different directions. A force with 2 newton metres pressure is applied to the testing during each of the 500 cycles and one cycle is where the handset is twisted once to the left and once to the right. A failure in this test is when the handset shows structural damage from the force of the test and all handsets need to pass the test for the batch to pass.
In the Drop Test, each handset is raised up and free dropped from a height of 1.4 metres on a slab of marble. The test is crucial to the R&D process as it checks whether the handset can survive being dropped and during the test, each of the six sides – the four edges, the back and the front – are tested to ensure they continue to work.
A key part of the drop test is the ultra-fast camera which records the drop at 5000 fps (frames per second) and allows them to replay the drop to see exactly where the fault in the handset is. An example of the type of faults that would be considered a failure is a cracked display, although it’s worth noting there is no guarantee against a cracked display.
Huawei R&D – the recap
If you’ve made it this far, thanks for reading as across the two parts, there’s a lot of information to take in. The tour of Huawei’s Research & Development building really indicated some of the ways that the company tests its handset and network businesses. It’s worth noting however that we were only shown a few of the thirty labs in the building and hence this isn’t a complete look at the R&D centre.
During the tour one thing was certainly apparent – the volume of tests is certainly expansive. In the device reliability testing room, there were over ten tests being run on handset reliability whilst in the environment and network labs, there were more than forty additional tests. Although the expansive test model does ensure reliability of a handset, it comes with a price as the average R&D process for a new handset can take five months (or longer as in the case of the Ascend Mate 7).
The testing process is quite exhaustive as to rule out anomalies in single cases, there are a total of 2000 – 3000 handsets tested at each round of iteration. It’s worth remembering that this not the Quality Assurance stage where the handset is tested for consumer use but the R&D stage where early prototypes are tested. The exhaustive R&D lab houses around 300-400 engineers at any given time, who are testing everything from antennae and performance to radiation and handset reliability.
Overall the tour of Huawei’s R&D centre revealed lots of new information about the R&D process which we’ve explained and summarised in this series. If you have any questions, do let us know in the comments and we’ll put them to Huawei to get an answer. If this interested you, head over to our Huawei Tour 2015 page where you’ll find the latest from our trip to China.
We’ll leave you with this:
People often accuse a company of copying another smartphone – think of two phones like the Galaxy Alpha and iPhone 6 who look-alike and launched at the same time – but the R&D process means the companies were probably just thinking along the same lines. Unless they had inside knowledge from the R&D centre, it’s virtually impossible could copy a handset and release at the same time.